不断的尺寸变化,不仅给电池和组件制造商造成投资困扰,也让很多客户不知所措。原则上通过增加硅片和组件尺寸,并不是真正意义上的技术进步,而且由于供应链和设备的关系,比如玻璃的宽度限制,层压机的极限,无限制的加大尺寸显然是不现实的。所以行业必须回到真正的制程工艺的研发,来提高单面面积的发电量,即能量密度上。晶科能源在其Tiger系列组件中首推的TR叠焊技术,让其在摩尔定律额阶梯上又上了一级。与硅片尺寸变化相比,TR叠焊工艺才是所谓的真正工艺进步,能在同样面积的硅片上提供10%的效率和性能增益,或将构成行业效仿的主流工艺之一。
效率和性能提升
在提高功率输出的同时,Tiger组件也创新性的采用了叠焊技术,细节图如下。晶科研发通过特殊工艺将电池片进行叠加,告别传统组件的电池片间隙,组件效率>20.7%。高功率+高效率,契合了“高能量密度”的组件发展趋势。
叠焊组件的关键技术点有三个:
1. 重叠区焊带减薄:Tiger组件使用了柔性的圆丝焊带,在重叠区域对焊带进行压扁设计,整体厚度低于非重叠区域和常规组件。
2. 重叠区焊带整形:整形后的焊带形状为变形的 ”Z” 字形,可以有效解决电池片重叠区域与焊带接触面积小的问题,防止碎片及不良。
3. 特制的EVA/POE层压后进行重叠区域填充:电池片串接完成后,在层压过程中使用特制的EVA/POE,高温下有效填充重叠区域电池片与焊带之间的缝隙,给电池片提供缓冲作用,保障组件可靠性。
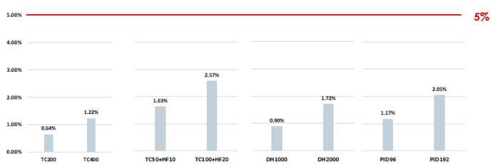
对于叠焊组件,晶科内部进行了严格的单倍/双倍IEC标准测试,结果如上图所示。
结果显示,单倍/双倍IEC标准的测试结果远低于IEC标准要求的5%功率衰减,甚至优于常规组件。叠焊技术在提效的同时,保证了组件优异的可靠性,确保客户电站30年稳定高效的运行。
Tiger组件在面积扩大的同时,亦保持了优异的载荷特性。在动态机械载荷测试中,通过在组件前表面动态施加±1000Pa的压力完成1000次循环,正面功率衰减率仅有0.6%,背面功率衰减率1.68%,远低于IEC标准要求的5%;在静态机械载荷测试中,将组件安装于载荷测试试验台上,对组件正面加压5400Pa,反面加压2400Pa,加压6次每次保持1h,正面功率衰减仅有0.3%,背面功率衰减1.82%,远低于IEC标准要求的5%。
谁会使用这一新工艺?
新的制造工艺并不适合每个人,但很明显,对于组件制造企业而言,在各种尺寸上押宝显然让自己陷入更被动的局面而加剧了硅片企业的寡头局面,对于设备新投资的风险也加大。所以只有掌握制程工艺,通过技术来提升效率才是竞争力关键,无论是什么尺寸都游刃有余。
TR叠焊技术无疑是在不增加设备投资,在现有产线上实现效率最大化的最可行的工艺。它既不受限于硅片尺寸和产能限制,又提升了能量密度,让同尺寸组件能塞入更多电池,目前部分一线厂家已经开始跟进晶科脚步,采用叠焊工艺,来满足客户接近摩尔定律边缘的需求。
责任编辑:肖舟