摘 要:新型无醇添加剂碱溶液制绒可使硅表面形成1~3 μm 的金字塔结构;通过对制绒过程研究,硅表面损伤层在250~500 s 被腐蚀掉,同时金字塔结构铺满硅表面,从500 s 延长至到1000 s 时,金字塔尺寸由1 μm 增大到2 μm 以上,1250 s 后金字塔尺寸达到平衡。不同添加剂配方可影响单晶硅表面的金字塔尺寸和均匀性,但对表面反射率影响不大。
0 引 言
晶面为(100)单晶硅片采用碱溶液可在表面腐蚀出金字塔结构,金字塔的倾斜面为(111)晶面,该过程被称为制绒[ 1, 2]。金字塔绒面的形成不仅会使硅片表面的反射率减小,还可在电池内部形成光陷阱,增加强入射光吸收效果,增大单晶硅太阳电池的转换效率。硅可与NaOH 等碱溶液反应在表面形成绒面,关于硅的各向异性腐蚀已有一系列研究,早期认为不同硅表面的悬挂键数目对表面的制绒起到关键作用[ 3, 4],(111)面的硅原子与最近邻表面的3 个原子形成共价键,(100)面的硅原子与最近邻的2 个原子形成共价键,(110)面的硅原子与最近邻的1 个原子形成共价键同时与表面的2 个原子形成共价键,其中密排晶面(111)结合力较强,相对较难腐蚀。后来通过对腐蚀过程的研究发现,硅表面不仅有H+的吸附,还有OH-的吸附;Vazsonyi 等[ 5]研究表明OH-在腐蚀过程中起到重要作用。碱环境通常采用NaOH、KOH、NH4OH 等溶液实现,反应温度控制在80~90 ℃[ 6]。如果采用纯碱制绒,OH-不断被消耗和硅酸盐不断产生的过程中往往发生剧烈反应,生成大量气泡,导致反应物OH-浓度减小,硅片表面无法与溶液充分接触影响制绒效率,容易造成金字塔尺寸的不均匀分布,从而致使制绒达不到理想效果。为了完善制绒技术,工业上一般通过添加硅酸钠和异丙醇(IPA)来抑制反应的进行[ 7, 8],控制反应速率,从而得到较好的绒面状态;异丙醇可抑制腐蚀产生的气泡,从而控制反应速度,但异丙醇沸点相对较低(82.45 ℃)、易挥发、对腐蚀过程中的温度控制要求苛刻、在腐蚀过程中还需根据消耗量不断添加,且异丙醇具有毒性,价格也相对昂贵,不适合大范围使用[ 9,10]。
近年来,无醇添加剂[ 11, 12]被研发并已用于大规模生产,无醇添加剂可促进Si 与OH-的接触速率,并得到小而均匀的金字塔结构,此方式是一种在工业上已被证明的稳定碱溶液体系,且具备较宽的工艺容差范围。无醇添加剂的成分主要包括阳离子表面活性剂、非离子表面活性剂、无水葡萄糖以及有机盐[13]、柠檬酸钠、去离子水和十二烷基苯磺酸钠等。虽然不同厂家会有不同添加剂配方,但制绒添加剂最终目的都是为了得到表面小而且均匀的金字塔绒面结构,提高制绒质量[14]。
1 实 验
首先用超声波清洗器清洗硅片,除去表面的油渍和沾污,然后采用无添加剂、异丙醇、A 与B型添加剂对比制绒效果,两种添加剂均为无醇添加剂。使用KOH 腐蚀溶液,其体积浓度为3%,添加剂比例为1.7%(V/V),反应温度为85±2 ℃,制绒时间分别为250、500、750、1000、1250 s。制绒后的硅片用HCl 和HF 的混合溶液进行中和处理,用扫描电镜对制绒后和经酸液中和的硅片分别观测。
2 结果及讨论
2.1 传统方法得到的结果
如图1 所示,硅片切割后表面会形成约5 μm的损伤层[ 15, 16],由于缺陷的存在,容易造成硅片表面少子寿命低、机械强度低等问题,在制绒前需将其完全腐蚀去除。
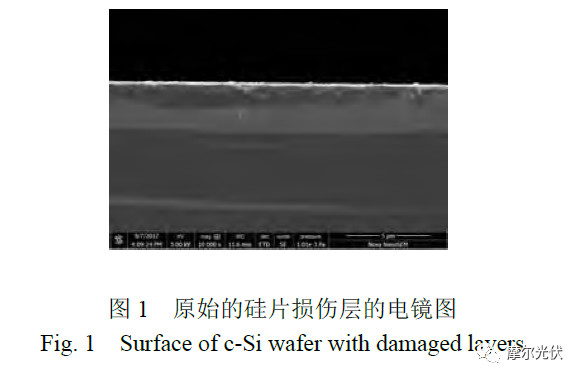
当损伤层被碱溶液腐蚀掉之后,完整的硅表面暴露出来,此时在单晶硅表面有零星散落的小金字塔形成。如图2 所示,随着腐蚀时间的延长,金字塔的数目逐渐增加,但在有限的腐蚀时间内(1250 s),金字塔并不能铺满整个硅表面,硅片表面大部分区域还未形成金字塔结构,且可看出形成的金字塔尺寸也不均匀。
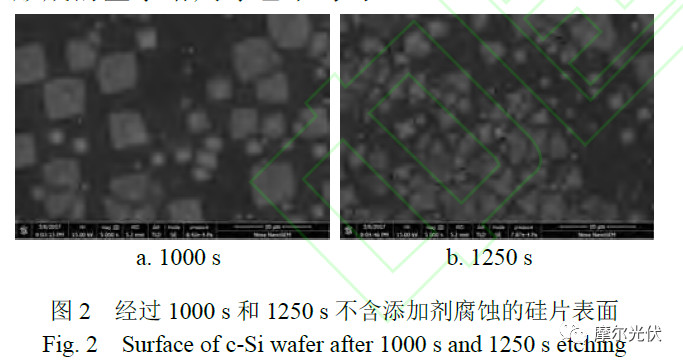
图 3 为在传统的碱腐蚀液中加异丙醇得到的硅表面形貌[17]。可以看出,制绒后的硅片表面铺满金字塔结构,但金字塔大小不一,大金字塔之间依附伴着许多小金字塔,此结构表明即使是异丙醇的碱液体系也很难有效调控单晶硅的表面微结构。
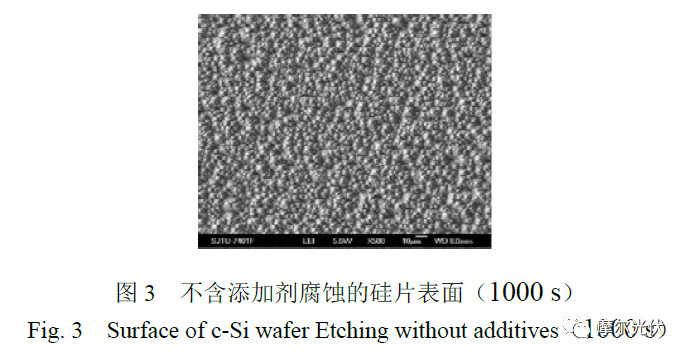
2.2 无醇添加剂制绒腐蚀过程
采用无醇添加剂,在实验中将腐蚀时间分别控制在250、500、750、1000、1250 s,观察硅片的表面形貌,如图4 所示。
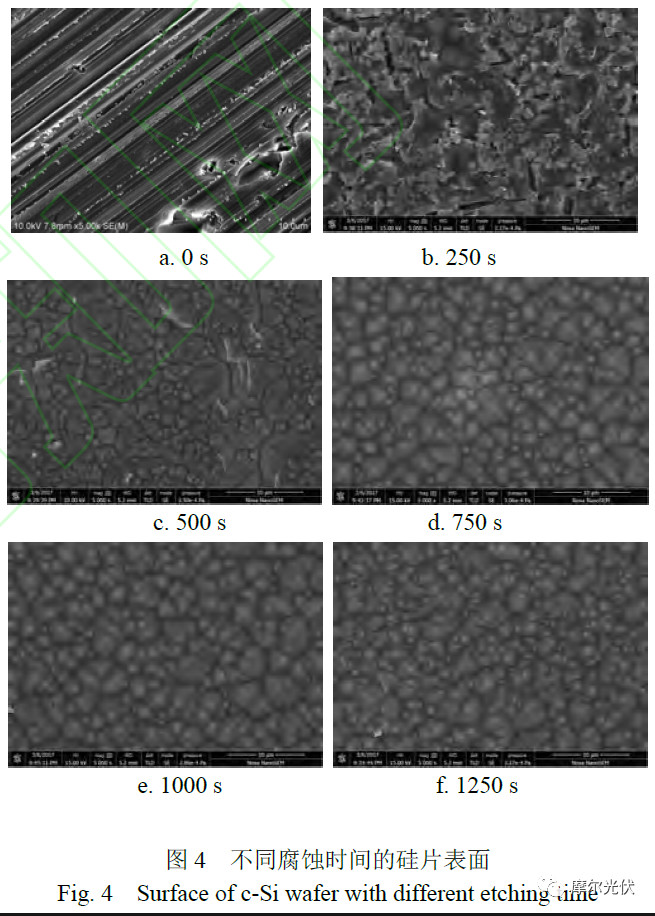