片间距不良,叠片是电池片焊接过程中的常见问题。以下为小牛自动化技术支持工程师高鑫为大家总结的相关处理经验,供大家参考。
1整片片间距不良时,首先要确认是否是连续串的前两片与第三片电池片间距不良还是无规律的片间距不良。
a) 连续串前两片与第三片间距不良的话,可以通过修改机器人串间距补偿值的Y数值进行修正。
b) 无规律的片间距不良则需要查看33部定位相机是否异常,如镜头脏污、焦距、光圈不合适等。
2处理叠片问题时,首先要观察压具位置是否正确,如果压具无法正常进入焊头的避让槽、压具回收手回收压具时不能正常拾取,则我们需要考虑:
a)后移动上下位置是否调节合适,当后移动上位过低时,会导致压具的磁钢与焊接台托条之间存在吸力,从而造成后移动向后搬运过程中压具受到吸力的影响无法正常伴随后移动向后运动;
b)后移动前后动作是否正常到位,该问题的判断可以在设定界面找到后移动前后电机的操作界面,然后在后移动零位、行程位分别做记号,多次往复运动后移动叉,查看是否每次都停留在标记处。
3当压具可以正常进入焊头避让槽、回收压具时可以正常拾取压具时,则我们需要观察叠片的电池片正面缩进是否正常:
a)如果正面缩进不正常,则表示在布片布带阶段就出现了问题,这时我们可以考虑查看定位相机是否异常、机器人放片位是否正确、H1低位是否过低等因素。
b)如果正面缩进正常,则代表布片布带时电池片位置正常,则可能是焊接过程或者焊接完成后向后一工位搬运过程中造成的叠片,比如焊带表面镀锡层较厚、焊接温度较高时,背面焊带化锡之后不能够完全冷却,在焊接完成后搬运过程中,多余的锡卡在焊台模组的导槽里,导致向后搬运过程中压具随着后移动叉运动,电池片留在原地不动的现象,具体可以见下图:
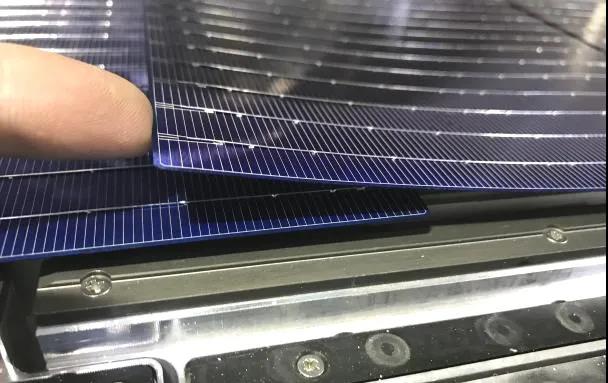
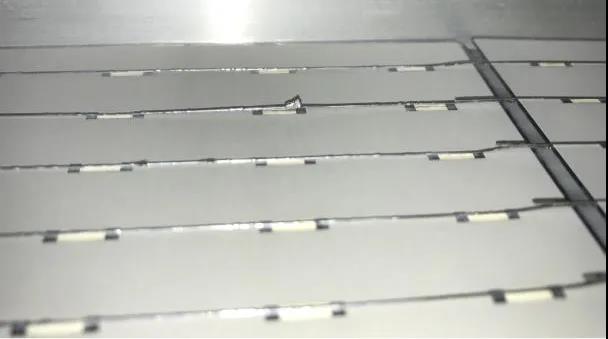
责任编辑:大禹