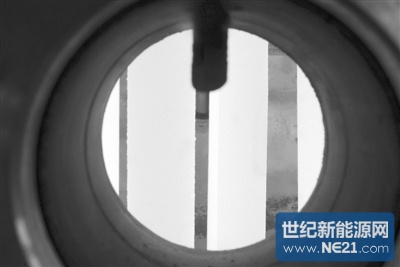
生产中的多晶硅
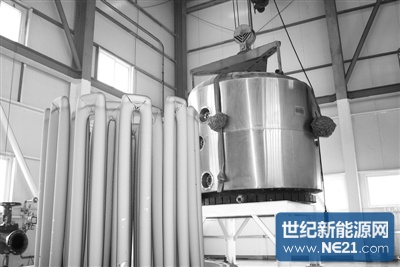
24对棒多晶硅还原炉装置
2013年1月18日,2012年度国家科技奖励大会召开。中国恩菲完成的“多晶硅高效节能环保生产新技术、装备与产业化”项目荣获国家科学技术进步奖二等奖。
在恩菲人看来,今日荣誉的取得,是一种认可——对多晶硅产业技术进步的认可;是一种回顾——追溯中国恩菲在多晶硅产业领域奋斗累积的十余年间,发挥技术优势,将产学研良好结合的每一段路途;是一种铭记——见证着中国多晶硅行业领军人物风雨兼程,为推动行业发展挥洒的青春汗水……
1月18日,人民大会堂。
在2012年度国家科技奖励大会的颁奖台上,由中国恩菲工程技术有限公司(以下简称“中国恩菲”)及其控股子公司洛阳中硅高科技有限公司(简称“中硅高科”)共同完成的“多晶硅高效节能环保生产新技术、装备与产业化”项目(以下简称“项目”)荣获国家科学技术进步奖二等奖。
这一奖项,是目前多晶硅行业获得的最高级别国家奖励,更实现了该行业在国家科技进步奖榜单上“零的突破”,而以严大洲、沈祖祥、毋克力、肖荣晖、汤传斌为代表的项目研发团队,也将为行业所铭记。
以试验示范线为起点,奠定技术基础
作为一种超高纯材料,多晶硅不仅是制造集成电路等半导体器件的关键基础材料,也是当今光伏发电产业快速发展的核心材料,更是国家鼓励优先发展的战略材料,关乎全球化解能源危机的成败。
多年来,我国由于缺乏先进的多晶硅生产技术,同时受制于发达国家的技术封锁和市场垄断,难以对自身丰富的硅矿资源进行充分开发利用,国内在产的多晶硅企业还因生产水平低、规模小、成本和单耗高、副产物难循环等问题而备受诟病。目前,国内的多晶硅几乎全部依赖进口,导致中国信息产业和新能源产业发展受制于人,举步维艰。
阻力重重,更加激发了中国恩菲硅材料研究团队发展多晶硅、振兴多晶硅的斗志和决心。自上世纪九十年代起,中国恩菲便将目光投向多晶硅产业:
1997年,中国恩菲以100吨多晶硅试验示范线为起点,探索改良西门子法的相关技术,为深入研究多晶硅生产技术积累经验;
2000年,中国恩菲率先在国内开展了多晶硅高效节能环保生产技术与装备研究,率先获得国家发明专利“四氯化硅氢化制备三氯氢硅方法”授权;
2002年,完成“年产2000吨三氯氢硅新技术产业化项目”,使自主研发的“合成产物加压冷凝技术、加压提纯技术和尾气干法回收技术”得以成功应用,并在节能环保方面取得显著成效,为今后建设万吨级生产线奠定了坚实的技术基础;
2003年,中硅高科成立,以中硅高科为载体,通过“研—产—电—硅”强强联合,中国恩菲迈开在多晶硅规模化生产道路上行进的脚步,为寻找安全、高纯、环保、低成本、大规模多晶硅生产工艺而执着追求,不懈努力。
以科研项目为依托,改变行业格局
2003年6月,中硅高科年产300吨多晶硅项目开工建设。当时国内还没有人实地见过如此规模的多晶硅生产线,一切几乎都是从零开始。中国恩菲多晶硅团队克服行业景气度低、融资困难等问题带来的重重压力,经过艰苦努力,在2004年成功研制国内首套12对棒还原炉,并于次年10月,迎来我国首条完全依靠自主研发技术,全部采用国产化设备建设的多晶硅生产线的顺利投产;
以年产300吨多晶硅项目为开篇之作,在国家部委和地方省市两级政府的大力支持下,中国恩菲和中硅高科承担完成了国家科技部863计划“24对棒节能型多晶硅还原炉成套装置研究”项目,该项目于2007年研制成功,单炉产量提高5倍,能耗接近国际先进水平;在此基础上,完成国家“十一五”科技支撑计划“24对棒加压还原炉”项目,成功研发第三代还原炉,单炉产量达到6吨以上,能耗指标达到国际先进水平;此后,又先后完成第四代、第五代还原炉的研发与产业化,成为国际单炉产量最高、单位能耗最低的节能工艺与装备,解决了多晶硅生产高能耗问题。技术推广后,使我国多晶硅规模提高了千倍,单炉产量提高10倍,能耗降低了66%,市场需求自给率达到50%。
与此同时,紧紧围绕世界主流工艺的发展,中国恩菲与中硅高科多晶硅研发团队开展了一系列科技攻关项目,共承担16项国家级科研与产业化项目。如,国家信息产业部“太阳能电池用多晶硅材料研发及产业化项目”,国家科技部“十一五”科技支撑计划项目“多晶硅材料产业关键技术开发”中“大型三氯氢硅合成、提纯工艺技术与关键装置研究”“高效加压还原炉系统研究”“大型低温加压四氯化硅氢化技术与装置研究”等三项重大课题,国家科技部“863”重点科技攻关项目“多晶硅副产物利用关键技术研究”。通过“高性能气相二氧化硅制备工艺技术研究”和“气相二氧化硅表面处理及尾气循环利用技术研究”两个课题,实现利用多晶硅生产副产物四氯化硅生产高品质气相二氧化硅的关键技术突破,成功建成年产2000吨生产线,在进一步延伸产业链的同时实现大规模多晶硅生产线中物料的完全闭路循环。此项技术不但能降低多晶硅生产的物料消耗,也从根本上实现了副产物的综合利用,真正实现多晶硅产业的节能减排和清洁生产。
历经十多年攻关,解决了一系列困扰行业多年的难题,中国恩菲在多晶硅高效节能环保生产的关键技术、装备与理论研究方面取得重大突破,最终形成了具有国际竞争力的技术和产品,消除了制约我国信息产业化和新能源产业的瓶颈。
以国家工程实验室为平台,引领行业发展
2008年,国家发改委批准在中硅高科设立“多晶硅材料制备技术国家工程实验室”——这是国家多晶硅材料制备技术领域的唯一一家国家级重点工程实验室。该实验室依托中国恩菲和中硅高科,联合清华大学等高等院校和国内多晶硅生产企业,共同研究突破技术瓶颈,培养、凝聚研发人才。按ASTM标准,实验室配备了先进的多晶硅检测仪器和分析工具,建设了包含氯硅烷分离提纯技术、多晶硅高效还原技术等在内的六个研发平台和一个测试分析中心,目前实验室已通过国家CNAS认证,形成了持续研发能力。针对制约我国多晶硅生产现状和需求,实验室开发研究大规模、低单耗、高品质的高纯多晶硅清洁生产工艺,形成了具有国际先进水平的千吨级以上规模多晶硅生产技术体系,提升了产业核心竞争力。此外,以该实验室平台为基础,中硅高科建设了国家多晶硅检测中心,通过了CMA计量认证,可对外提供检测服务,涵盖多晶硅生产的原料、中间物、产品、环保类等58个大项检测,服务全行业。
依托国家工程实验室,研发团队紧紧围绕“多晶硅高效节能环保生产新技术、装备与产业化”专题,共申请专利97项,其中16项国家发明专利、21项实用新型专利获得授权和152项技术诀窍,完成5项成果鉴定,有效实现了多晶硅技术的创新与专利保护同步发展。
自主创新引领技术进步的过程中,研发团队还主编了我国首部《多晶硅企业能源消耗限额》《太阳能级多晶硅》和《多晶硅工厂设计规范》等3项国家标准,建立了能耗和质量控制要素、技术指标和评定方法,提高了我国多晶硅行业标准化水平,进一步完善了行业标准体系,为多晶硅产品升级、安全生产和节能减排提供了技术支撑,为民族多晶硅产业发展做出了突出贡献,带动了太阳能光伏和相关制造业的发展,实现了显著的经济、社会和环境效益。
以节能降耗为重点,实现技术突破
中硅高科采用当前多晶硅生产的主流工艺改良西门子法生产多晶硅,以节能环保为出发点,以产品品质为核心,以节能降耗为理念,结合现有工艺流程,不断优化工艺路线。项目负责人严大洲表示,总结中国恩菲和中硅高科的技术创新成果,重点、亮点非常多,首先是通过节能技术解决了多晶硅生产的高能耗问题。
高纯多晶硅的生产过程,是将高纯三氯氢硅用高纯氢气还原成高纯多晶硅的过程,其能耗占总能耗约50%以上,是实现多晶硅生产环节节能降耗的重点。
大型节能还原炉系统是实现大规模化生产多晶硅产品的关键技术之一,是解决多晶硅大规模生产、成本低廉、提高产品质量的根本途径。中国恩菲多晶硅研发团队首次创立节能还原炉系统设计方法,通过模拟优化,大幅提高多晶硅节能还原炉单炉年产量,其核心技术装置第五代还原炉已成功应用生产,达到国际先进水平。在此基础上,还在研发36对棒、48对棒、60对棒大型节能多晶硅还原设备及加压还原工艺技术,为万吨级多晶硅生产线和节能技改提供技术支撑,具有重大的市场价值和良好的产业化开发前景。同时将整个多晶硅工程的各种能源要素通盘考虑,冷热综合利用,为多晶硅低成本、低能耗经济运行创造条件。
以绿色环保为目标,为多晶硅正名
多晶硅还原尾气主要含有氢气、氯化氢、三氯氢硅、四氯化硅等成分。由于过去通常采用湿法回收还原尾气,工艺消耗大、收率低、生产成本高,一段时间以来,多晶硅行业一直被冠以“高排放、高污染”的“罪名”。对此,专家表示,对行业的判断应从实际出发、从国家能源战略的角度出发。多晶硅生产中是否会造成污染,与生产技术和工艺密切相关。
中国恩菲及中硅高科研发团队开发了大型还原尾气干法回收系统技术,充分利用尾气中各组分物理化学性质的差异,首创具有自主知识产权的“加压鼓泡淋洗-吸收-脱吸-活性炭吸附”的多晶硅尾气分离回收利用新工艺;
成功研发并建立具有自主知识产权的吸收塔、脱吸塔、活性炭吸附器等特殊结构的大型装置,实现单条还原尾气处理能力满足年产5000吨及以上规模多晶硅建设项目配套需求。
目前,国内首套大型还原尾气干法回收装置已经成功应用于中硅高科各条生产线,从运行结果看,氯硅烷、氢气、氯化氢气体利用率分别达到98.5%、99%、99%以上,使多晶硅生产过程中纯氢消耗从传统西门子工艺的近35立方米/千克降至1立方米/千克以下,且系统能够适应多晶硅生产能力的变化,从根本上控制“三废”排放,减少多晶硅原料消耗30%,降低多晶硅成本,实现了清洁、无害化生产。
以降本增效为导向,突破技术瓶颈
据统计,每生产1吨多晶硅产品将产生副产物四氯化硅10余吨,对其的回收利用直接影响环境、安全及企业效益。当前主流处理工艺是将其氢化转变为三氯氢硅,成为多晶硅原料,返回系统使用。
通过小型、半工业试验,中国恩菲从工艺上实现了将多晶硅生产过程中产生的四氯化硅向三氯氢硅的转化,少量不能氢化返回的低品质四氯化硅经提纯后用于气相白炭黑生产,副产物循环利用率99%以上,多晶硅生产成本降低35%,通过物料的闭式循环利用,有效解决了多晶硅企业规模化生产的瓶颈问题。
中国恩菲将创新技术集成后,在中硅高科实施产业化。运行结果表明,首创的低温加压氢化生产工艺、创新研制大型低温加压氢化装置和活化、氢化氢气回收技术,在反应条件、处理能力、一次转化率和单位产品电耗方面都显著优于当时国外氢化技术,达到国际领先水平。该工艺通过加压、吸附、净化系统,将活化、氢化的尾气中氢气全部回收,使其返回系统后循环使用,利用氢化高温反应产物能量加热进入反应器的反应物料技术,降低能耗水平达30%。
据了解,近几年来,中硅高科除了应用低温氢化技术处理自身副产物之外,还处理了来自国内多家多晶硅生产企业的副产四氯化硅,为行业协同发展做出了重要贡献。目前,多晶硅行业形势艰难,国内一些企业停产技改,纷纷采用低温氢化技术,期望通过此举能够有效降低生产成本,提高我国多晶硅产品的竞争优势。以全国10万吨/年的多晶硅产量计算,若实现副产的100—200万吨四氯化硅的全部氢化,将产生40—80亿元的经济效益,推广前景非常广阔。
另一方面,多晶硅纯度是衡量产品品质的关键因素。中国恩菲从提高原料三氯氢硅的纯度入手,聚焦于产品质量的提升。
中国恩菲发明了三氯氢硅合成、高效筛板与填料组合的加压精馏提纯技术,单套高纯三氯氢硅分离能力为当时国内先进水平的10倍,提纯后三氯氢硅指标优于国内先进水平2倍以上,且能够满足电子级多晶硅纯度要求;发明大型高效、加压、高温三氯氢硅提纯工艺,减少蒸汽消耗和塔顶循环水消耗,降低能耗45%;创新研制大型三氯氢硅加压合成装置,单套系统年产能高出国内最好水平2倍以上,合成产物中三氯氢硅含量、氯化氢综合利用率和硅粉利用率,分别高出国内最好水平10%、9.1%和18.6%,达到国内领先水平;创新研制了合成产物加压分离和尾气全回收工艺,回收的氢气和氯化氢气体返回生产系统,从根本上解决环境污染问题,显著降低成本。
以产业化成果为助推,彰显行业责任
2005年,中硅高科年产300吨多晶硅生产线正式投产,标志着多晶硅规模化生产技术体系形成,打破了国外多年的技术封锁和市场垄断。2006年中国多晶硅产量达到286吨,同比增加257%,国外的单项技术和设备开始进入中国。
此后,中硅高科以中国恩菲雄厚的技术实力为依托,在2006年至2011年之间,创造了在国内率先实现千吨级多晶硅生产规模、建成投产国内最大的单条多晶硅生产线的骄人纪录。目前,中硅高科已形成具有中国特色的“物料闭路循环、热量综合利用”多晶硅清洁生产工艺路线,拥有万吨级多晶硅生产规模,位居世界前十位,技术水平和生产成本、产品盈利能力达到国际先进水平。2011年,我国多晶硅产量8.3万吨,首次超过欧美,成为世界多晶硅生产大国,改变了世界多晶硅格局。
严大洲说,这次在国家科技进步奖励大会上获奖的“多晶硅高效节能环保生产新技术、装备与产业化”项目的发展,实际上,就伴随着中国恩菲、中硅高科的发展历程。今日荣誉的取得,是一种认可,是对行业产业技术进步的认可,是对中国恩菲和中硅高科多晶硅团队不懈钻研,执着进取的高度奖赏;是一种回顾,追溯了中国恩菲在多晶硅产业领域奋斗累积十多年,发挥技术优势,将产学研良好结合的每一段路途;荣誉是一种铭记,见证了以严大洲为代表的中国多晶硅行业领军人物风雨兼程,为推动行业发展挥洒的青春和汗水。
艰难困苦,玉汝于成。
刚刚过去的2012年,是我国多晶硅—光伏产业发展历程中最艰难的一年:美、韩、德等国对上游多晶硅市场实施大幅低价倾销策略,严重影响企业生存;光伏终端产品遭遇美欧“反倾销、反补贴”调查,形成毁灭性打击;受金融危机、欧债危机影响,各国下调光伏补贴电价,削减装机规模,下游市场急剧萎缩,……面对企业库存积压、大面积亏损和减产、停产,甚至破产的艰难境地,曾有人用“哀鸿遍野”来形容行业发展的严峻形势。
破解光伏产业困局的重要手段之一,是全面启动国内市场。严大洲说,从国家战略上看,光伏产业属于国家能源战略的一部分,能源战略,尤其是发展清洁能源战略,是未来国家长久、稳定发展的根本性战略。光伏产业的前景非常广阔。当前,随着国家一系列政策的出台,我们已经看到国家大力发展光伏产业的决心。未来,伴随政策落地,企业将迎来新的发展机遇。
挑战也是机遇。中国恩菲仍然致力于通过技术改造和持续研发,以多晶硅制备技术国家工程实验室为平台,以中硅高科产业为基础,不断降本降耗,提升品质,节省投资。在研发了低温氢化第六代技术和第五代还原炉之后,36对棒、48对棒、60对棒还原炉、硅烷法流化床反应器等研究开发仍在进行,也希望通过更先进的装备,实现更大规模生产,实现行业技术水平的新跨越。
在中国恩菲多晶硅研发团队的心里,荣誉更多的意义,是认可,是国家对所有为多晶硅行业的每一位从业人员和他们的家属所付出的共同努力和奉献的认可;荣誉也是激励,为寒冬中的多晶硅产业带来了希望和温暖。
期待,以荣誉为动力,坚定行业同仁发展的信心。
期待,以荣誉为起点,我们共同努力,迎来中国多晶硅产业的春天。
责任编辑:solar_robot